History of Lean
Lean focuses on stability and elimination of Waste. Lean Manufacturing began with Henry Ford by lining up fabrication steps in process sequence using Standardized Work and interchangeable parts. Ford called this ‘Flow’ production (1913). In the 1930s, and more intensely just after World War II (1950), Kiichiro Toyoda, Taiichi Ohno and others at Toyota started looking at Ford’s situation. While Ford was producing 8,000 vehicles per day, Toyota had produced only 2,500 vehicles in 13 years. Toyota wanted to scale up production but lacked the financial resources required for the huge quantity of inventory and subassemblies as seen at the Ford’s plant. What impressed Ohno even more than the visit to the Ford factory was the visit to the ‘Piggly Wiggly’ supermarket. At that time, Japan did not have a supermarket where customers could pick up their products themselves and where the stock on the shelves was frequently replenished from the warehouse. This process inspired Ohno to set up production in the Toyota factory in the same way and only produce what the next process needed. Toyota developed its famous ‘Toyota Production System’ (TPS) to avoid the problems and high costs of large inventories. TPS includes some of Ford’s ideas, but also incorporated the philosophy of ‘Just In Time’ (JIT) and ‘Pull’, based on Piggly Wiggly’s supermarket concept.
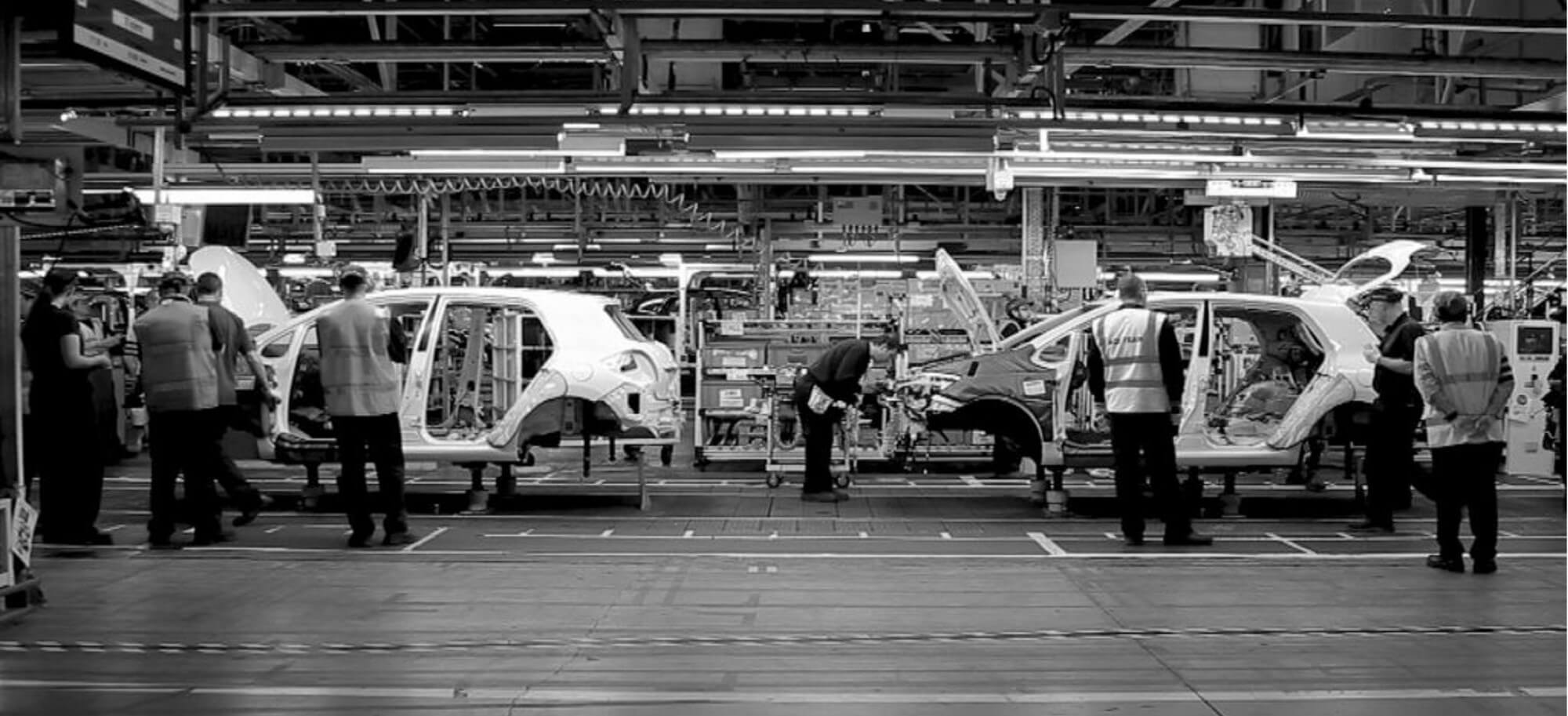
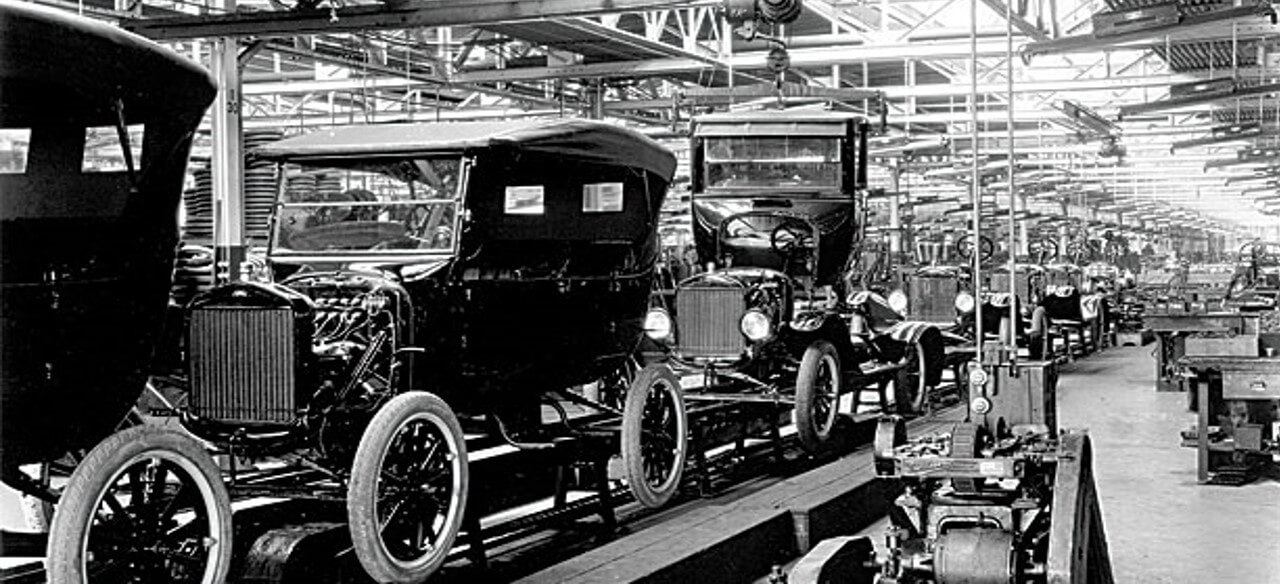
In 2008, Toyota became the world’s largest auto manufacturer in terms of overall sales. Over the past two decades, Toyota’s continued success has created an enormous demand for further knowledge concerning Lean Thinking. There are literally hundreds of books, papers and other resources currently available to this growing Lean Management audience.
The Lean thought process is thoroughly described in the book ‘The machine that changed the World‘ (Womack and Jones, 1990) and in a subsequent volume, ‘Lean Thinking’ (1996), which specifically describes the five Lean principles. The concepts of Lean have been widely distributed around the world. Lean principles and tools are being applied in production, logistics and distribution, services, trade, health, construction, maintenance and even in government with the common goal of reducing turnaround time and operational costs while at the same time improving quality. One of the most important activities within Lean programs is the identification and elimination of Waste, also called ‘Muda’. Within a value stream eight types of waste can be distinguished: over-production, waiting, transport, over-processing, inventory, movement, defects and unused expertise.